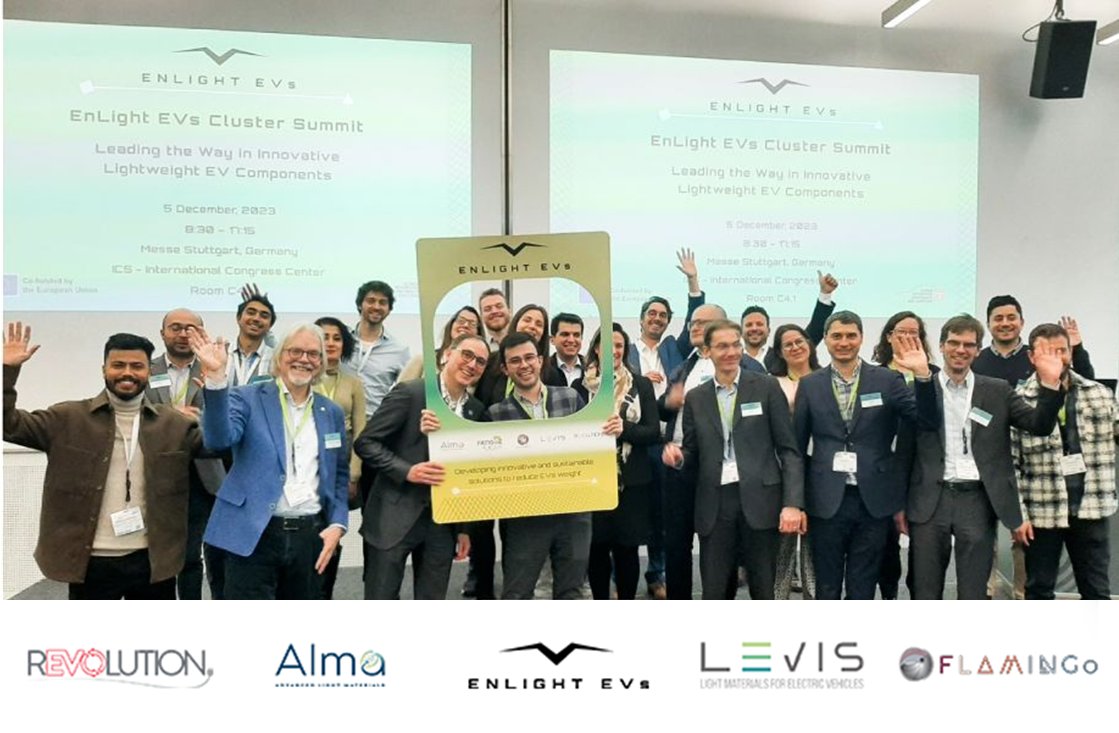
After months of preparation and hard work, the Enlight EVs cluster disseminated project results and showcased physical demonstrators of their novel electric vehicles at the Global Automotive Components and Suppliers (GACS) Expo in Stuttgart, Germany. This annual automotive event, held from December 5-7, 2023, features cutting-edge manufacturing expertise from across the world. Thus, it served as the ideal platform to enhance engagement with an industry audience and create visibility around lightweighting electric vehicle components.
Created in December 2022, the cluster is a group of five EU-funded projects under the Horizon 2020 Research and Innovation programme to find synergies and maximise impacts across the European Union (EU) and beyond around lightweighting EV components.
The five projects in the cluster – ALMA project, Greenvehicles LEVIS, Fatigue4Light, FLAMINGo project and REVOLUTION project – aim at developing innovative solutions, tested in industrial pilots, that can be rapidly applied in the automotive market to reduce the weight of electric vehicles (EVs), while considering structural integrity, passengers’ safety, and sustainability, through eco-design and circular practices.
To further this objective, the cluster planned and participated in the final technology transfer event titled “Leading the way in innovative lightweight EV components” at the GACS Expo, in which the projects presented their respective results to the cluster and industry audience in the presence of our esteemed guest of honour Salima Abu Jeriban, Project Adviser to the European Commission (CINEA). The central goal was to facilitate technology transfer and knowledge exchange among cluster partners.
Salima provided concise introductions for all the projects, offering insightful summaries. Finally, she concluded the session with impactful closing remarks. The presentations were followed by panel discussions, which was an opportunity for the members of the audience to ask the project representatives questions about their innovations.

Salima actively engaged in these discussions, focusing her questions on the practical applicability of the presented technologies and the future roadmap. For example, during the Greenvehicles LEVIS project panel discussion, Salima asked if they have some technology that can be directly applied in electric vehicles.

Agustin Chiminelli, R&D Composites and Adhesives, from ITAINNOVA answered: “Overall, we have a specific activity related to the exploitation plan, it is not completed yet but some of the results are closer to market uptake and exploitable soon, while some others are a bit far.”
Following that, ALMA presented project results under the theme “Sustainable Lightweighting: Redefining the Future of E-Mobility with Circular Design and Advanced Materials for Passenger EVs.” The project was briefly introduced by the EU Commission Project adviser (CINEA) before Raquel Ledo, the ALMA project coordinator, gave an overview of work done by CTAG – Centro Tecnológico de Automoción de Galicia in the project and results.
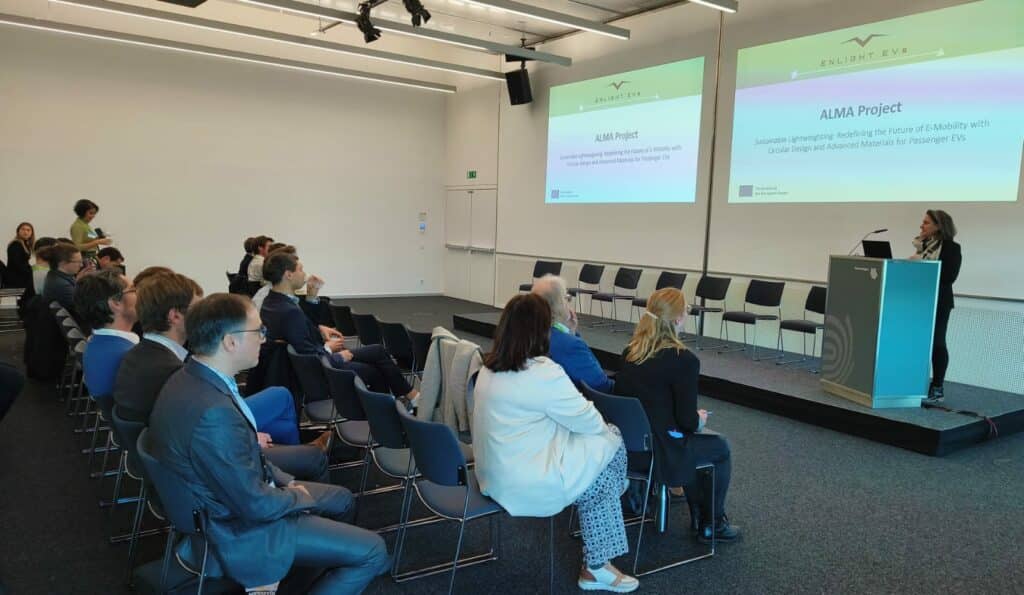
Raquel emphasised that EV projects need to think of end-of life of vehicle and materials, especially with regards to efficient and low-cost material separation in multi-material platform. “We need to redesign, but we can’t forget that we need to fulfill the technical requirements to meet safety and performance, but we are also thinking about end-of-life of vehicles in which we have considered how to separate these materials in a multi-material platform,” she said. At the same time, Raquel added, systems thinking is applied in the ALMA project.
“Cost is important and all the innovations should be affordable, otherwise is it not valid for us.”
Raquel Ledo, CTAG, ALMA project coordinator

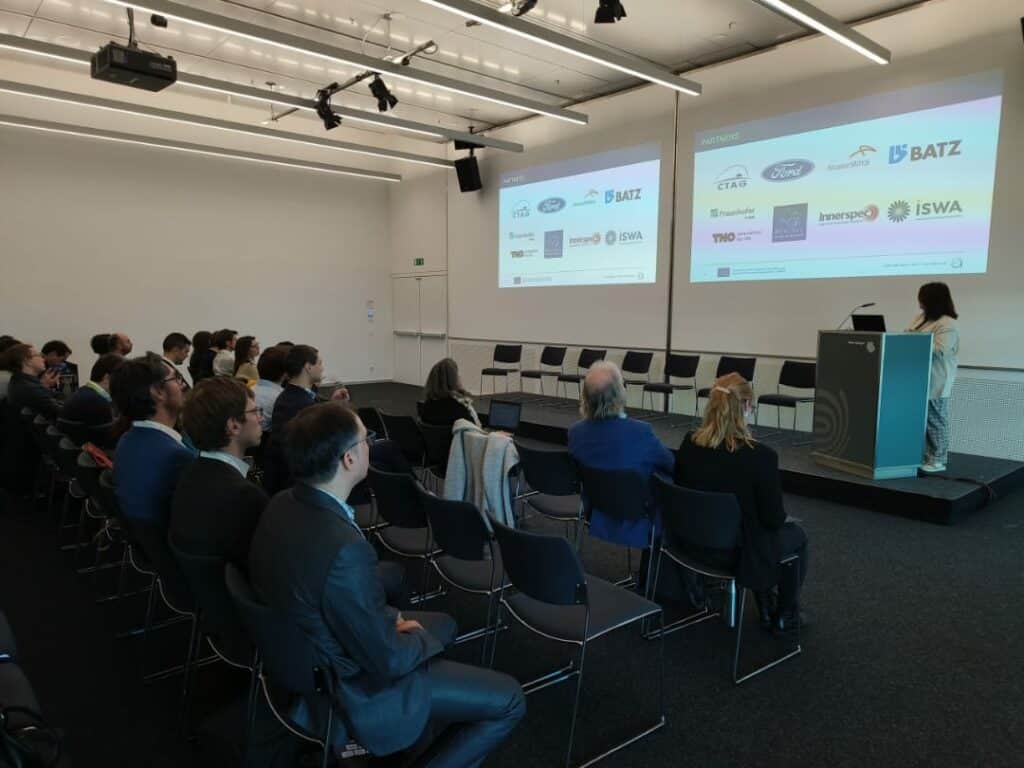
Vanessa Ventosinos Louzao from CTAG then followed suit by delving into the ecodesign approach, which informs the ALMA lightweight novel battery electric vehicle. She said the eco-design approach has been applied throughout the entire life cycle to create a multi-material BEV structure, optimising material selection and production processes for efficiency and environmental sustainability. As a result, the body-in-white (BiW) of ALMA’s concept car is 160 kg lighter, representing a 22% weight reduction compared to the baseline BEV BiW. Over the car’s entire service life, the use of other materials and weight reduction contributes to a total reduction of 1850 kg CO2 eq., a 24% decrease in emissions.


From ArcelorMittal, Jerome Favero, Head of automotive steel solutions, Global R&D, discussed advanced materials, such as advanced high strength steels (AHSS) and steel laminate materials used for lightweighting and structural integrity. He said the primary objective behind developing and finetuning of advanced steel materials was to achieve substantial mass savings while maintaining comparable crash performance, before briefly explaining materials, such as FortiformS1270 (AHHS), Duplex (steel with reduced density) and Ultimate (a sandwich of steel/plastic/steel laminate material), among others.
Two of their validated concepts, H-Frame and Door Ring, which employ a Multi-Part Integration (MPI) technology with a single hot stamping operation, highlighted the efficiency in manufacturing process. These demos were displayed at the Expo.

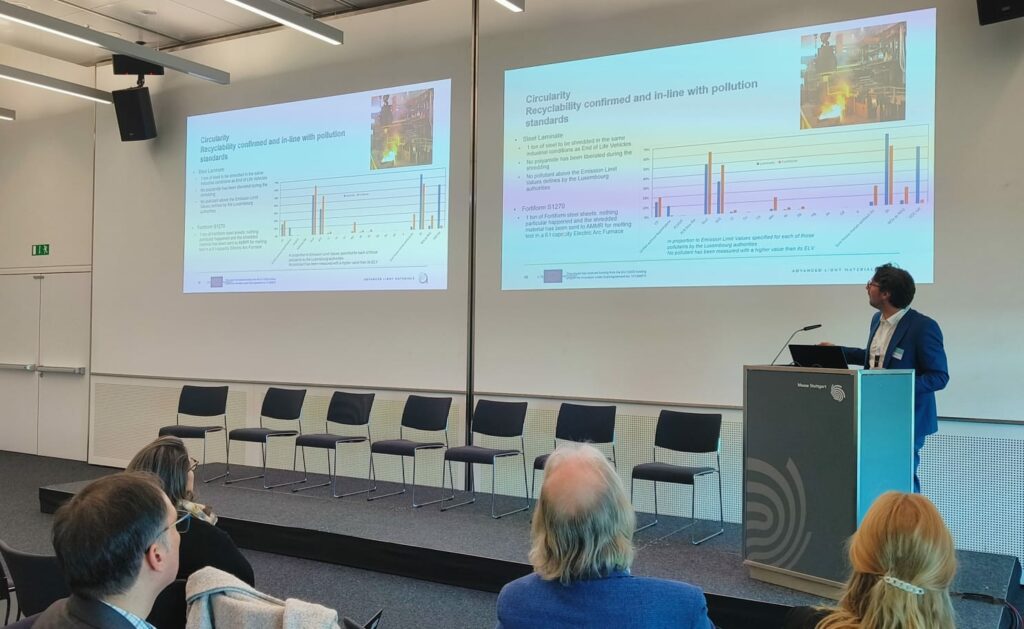
Hannes Grimm-Strele from Fraunhofer ITWM explained the experimental and simulation models for SMC materials at multiscale level to verify the vehicle’s structural integrity, among other things. Hannes stressed upon the need to determine fibre orientation in SMC material through mechanical simulation, with the “aim to keep experimental effort as low as possible and then use the virtual tests and computer simulations to give us the calibration data in two steps: microscale and mesoscale.”
During the Q&A session, Salima posed a question for Hannes: “How did you test the influence of the textile reinforcement?”, to which he replied, “We performed bending tests with two variants. We generated mesoscale models with different textile volume contents and calibrated material cards which could reproduce the bending tests with good accuracy.”


Finally, Dr. Tom Ligthart from TNO showcased BEVSIM, the LCA and LCC tool, and its practical applicability, urging the audience to try it out for their respective projects to measure environmental impacts associated with material choices.
After the presentation, Salima enquired about the weight comparison between ICEV and ALMA BEV and its implications on vehicle range. She also asked about the type of databases that BEVSIM tool relies on and update frequency. There was engagement from the audience too, one of whom asked about BEVSIM’s ability to handle scenarios where materials come from one country, like China, but the car is sold in another, such as the US.

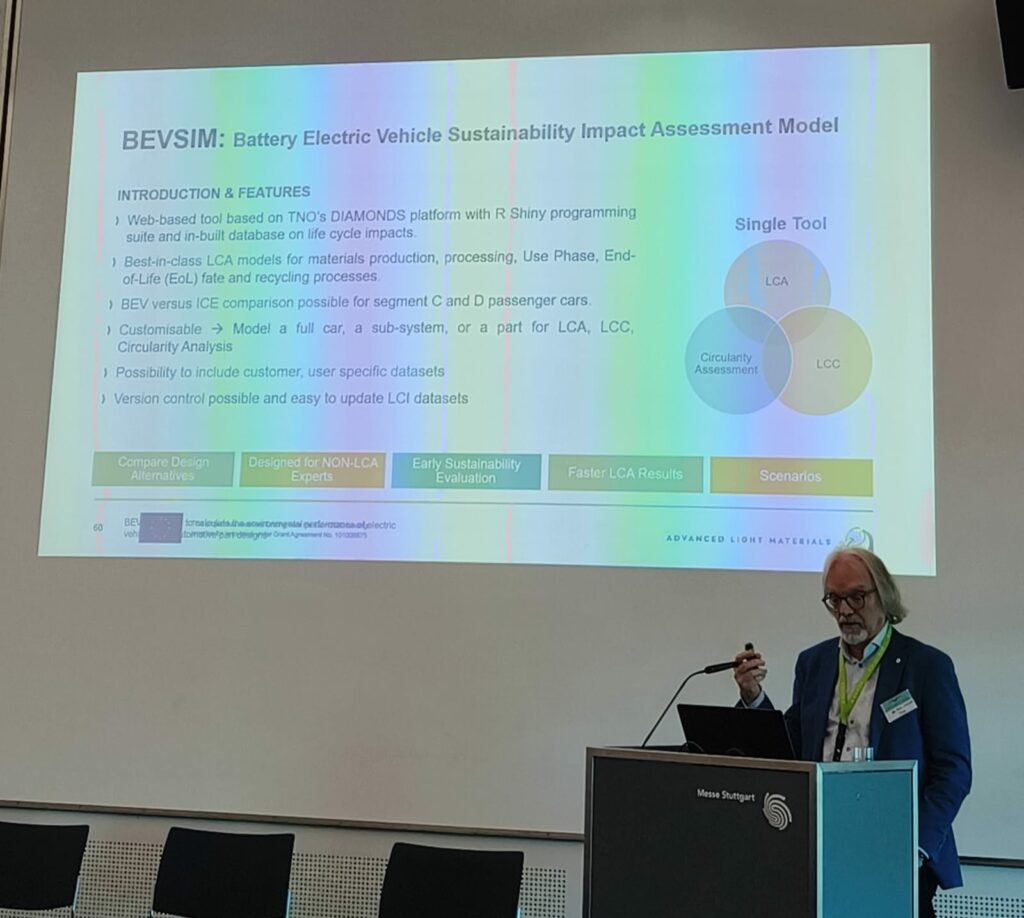
Following the presentations, Jose Uribe from the International Solid Waste Association (ISWA), also dissemination partners in the ALMA project, moderated a panel discussion with ALMA consortium members, including TNO, ArcelorMittal, CTAG, Ford and Fraunhofer ITWM.

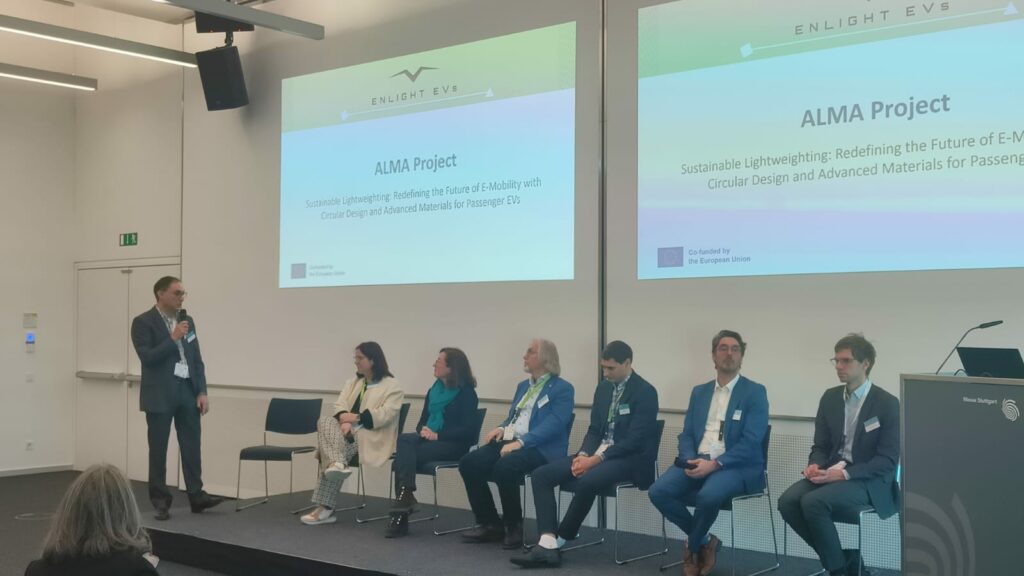
Various themes were discussed during and after the panel discussion. From the EU’s End-of-Life Directive and its compliance by the ALMA project to a discussion on the growing demand for LCA by automotive manufacturers, diverse themes were investigated by consortium partners, in the presence of Salima, who brought the EU’s policy perspectives on sustainable e-mobility.
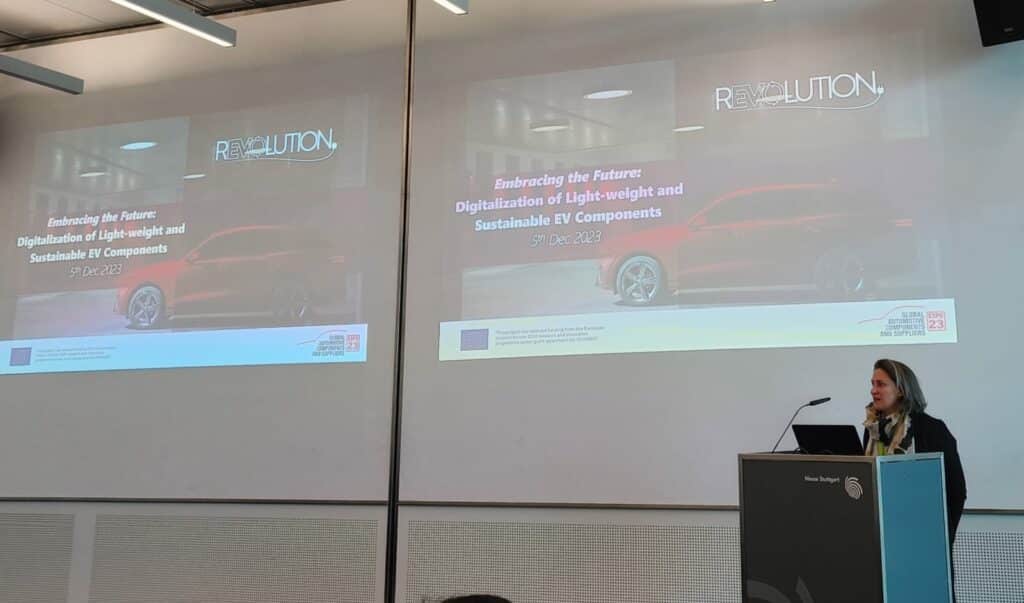

In connection with new EU regulations in the past year, Raquel briefly discussed the trend of OEMs asking for quotations for standard materials but also demanding an ecological answer, such as Life Cycle Assessment tools to measure environmental impacts of vehicle structure.
Vanessa from CTAG echoed Raquel’s point of view: “There is a shift in the conception of new cars; engineering offices have Eco-design approach in mind now. In the last five years, all our clients have asked for ecological options. In this case, the design is the very first step in order to make sense of the end-of-life solutions.
Indeed, end-of-life solutions and multimaterial approach should be incorporated in the design phase. During the panel discussion, a question was posed to Ilya Popov from Ford-Werke, one of ALMA’s consortium partners and OEM, on multimaterial approach, and he said, “when we talk of multimaterial approach, we need to change the design. We need to enhance new technology and design so that at the end-of-life, we can take the parts apart, sort it, recycle and reuse the parts. Thus, multimaterial approach should go hand-in-hand with new design.”
This growing eco-rationale is also embedded in the ALMA project, as our novel BEV is informed eco-design and circular approach, in which we used the right materials in the right place for the right application and designed for assembly/disassembly and recycling.
TNO’s Dr Lighart also brought to focus the BEVSIM’s capabilities to measure the impact of materials used in the ALMA vehicle on the environment, but also said that “other environmental impacts are also important to measure aside from carbon footprint, which the BEVSIM takes into account.” In that sense, BEVSIM takes a very holistic perspective of environmental impacts.

Subsequently, in her closing remarks, Salima congratulated the Enlight EVs cluster for facilitating knowledge transfer between the sister projects but also executing the final cluster dissemination event at the GACS Expo for wider visibility and engagement with external audience.
With regards to ALMA, Salima found the eco-design approach in the project appealing but also that the project practically responds to the EU policy landscape on circular economy and sustainable e-mobility.
In a conversation with Salima, she said “the particularity of the ALMA project is the ability to think about the parts of the vehicle by reflecting on the end-of-life of the vehicle, and then taking that into account to have in mind the best way of designing those vehicles. When we think about the materials and how to create, mould or assemble them… what is also interesting is to also reflect one each material for each use (sic).”
“The best thing is that the ALMA project has an OEM (Ford-Werke) to guide the process, so you actually had your wheels on the ground.”
Salima Abu Jeriban
Enlight EVs Booth Participation

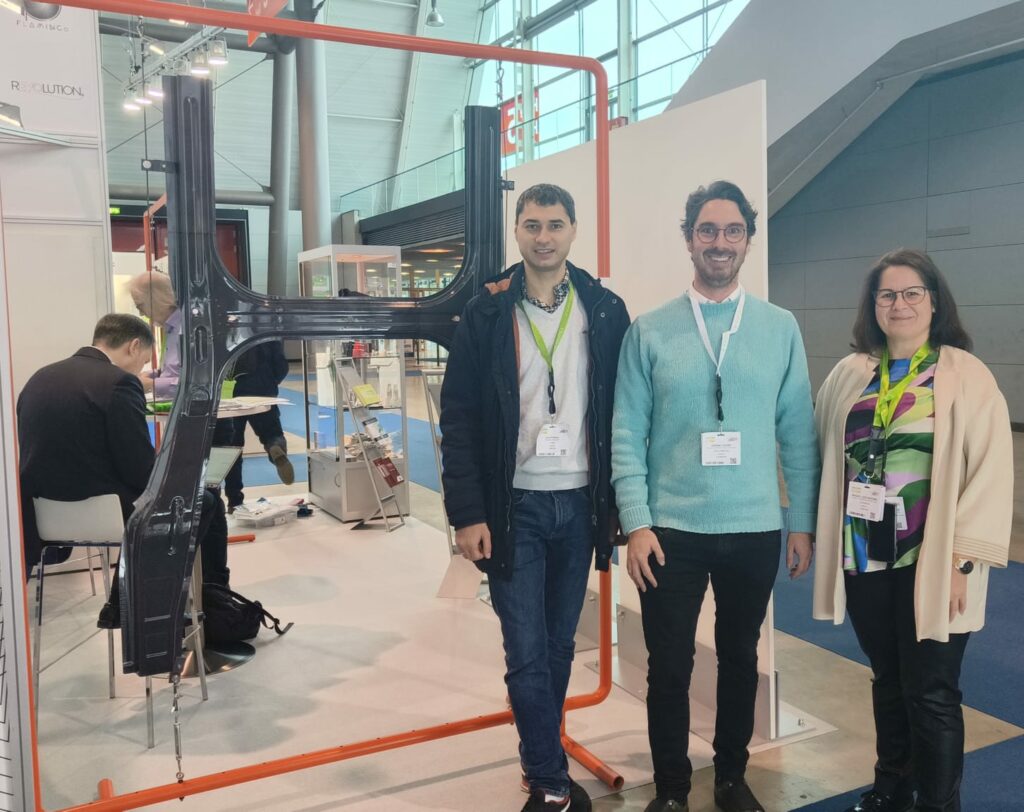


On the other side, cluster booth number 5300 in Hall 5 was abuzz with activity. Our booth witnessed a steady stream of curious visitors who enquired about the demos displayed, including the innovative H-Frame and Door Ring by ArcelorMittal from ALMA project.
Over the next few days, we had several visitors, mostly automotive components and vehicle manufacturers, including BYD (China), Toyota (Japan) and Ford Motor Company, asking questions on the value savings and technology used in the H-Frame and Door Ring.
Understandably so, because the innovative H-Frame and Door Ring utilise MultiPart Integration (MPI) tech, Laser Welded Blank (LWB) technology and advanced press hardening steel grades. What’s more, while the H-Frame transforms the traditional 11-parts made of conventional steels into a single component, the Door Ring reduces 36 parts into four, simplifying production by minimising forming and welding operations.
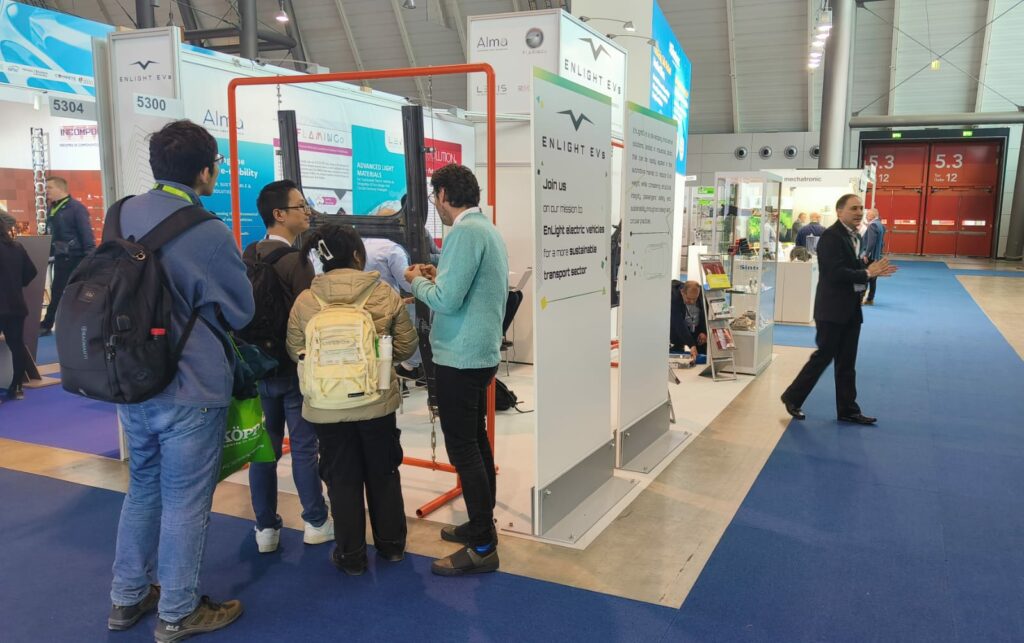


What kind of technologies do the H-Frame and Door Ring incorporate in the ALMA project?
Both product innovations use a combination of Multi-Part Integration (MPI) concept, single hot stamping process and Laser Welded Blanks (LWB) technologies. These processes combined optimise crash performance, achieves greater weight reduction, maximises material utilisation and contributes to sustainability by reducing Carbon emissions in steel production.
In the second picture, on the right, members of organisation called BYD, one of the biggest in China for EV production, asked our booth representative Jerome Favero from ArcelorMittal about the technology used in the H-frame and the value saving involved in its application in EVs!
The H-Frame and the Door Ring were among the many other exhibits at the booth, which was collectively shared by sister projects REVOLUTION, Greenvehicles LEVIS, and FLAMINGo.
The cluster, funded by the European Commission under the Horizon 2020 programme, aims to make the transport sector more sustainable by developing innovative solutions around lightweighting EV components that can be rapidly applied in the automotive market in order to transition to a circular economy.
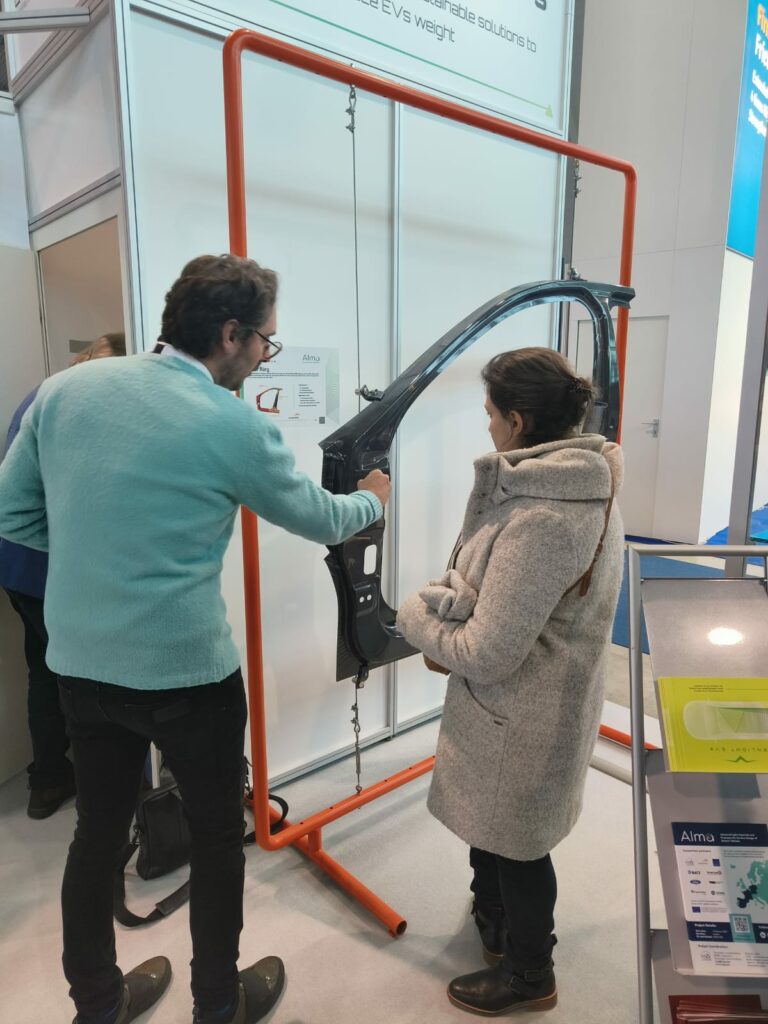


In general, expo visitors expressed interest around lightweight EV components but also around battery and EV Range! On that front, the Enlight EVs cluster – REVOLUTION project, Greenvehicles LEVIS, FLAMINGo Project H2020 together and individually explained their respective projects objectives and demos on display.
For ALMA, most queries were related to the materials and technology used in the H-Frame and Door Ring, the two exhibits from ArcelorMittal, and the kind of value saving that businesses can achieve with this innovation. Some queries were also on the hot stamping technology used in H-Frame and Door Ring in order to minimise manufacturing processes, materials usage and time.
Curious visitors were also seen knocking on the Advanced High Strength Steel (AHSS) twice, thrice to ensure if what they were feeling was real at the Global Automotive Components and Suppliers Expo!
Pat came the reply from our booth rep, Abhimanyu Chakravorty from the ALMA project: “Ingenious isn’t it? This is from our consortium partner ArcelorMittal,” he said.
Over the last 3 days, the H-Frame and Door Ring captured the interest of visitors due to its contribution to lightweighting and minimised references during manufacturing process.


Other sister projects, such as Greenvehicles LEVIS, received questions from FORD Turkey on aluminum parts used in their project.
For example, Cem İÇİER from Greenvehicles LEVIS received queries around lightweighting, and he explained how material change in the steering column carrier group led to weight reduction!

Here’s what he said to the visitor: “For the cross car beam part of LEVIS electric vehicle, I explained how we changed the materials for the steering column carrier group from steel to composites for lightweighting and how it decreased manufaturing complexity. The weight reduction achieved for the carrier group is 28%.”
FLAMINGo Project H2020, on the other hand, received queries around their physical demos, such as the steering knuckle.
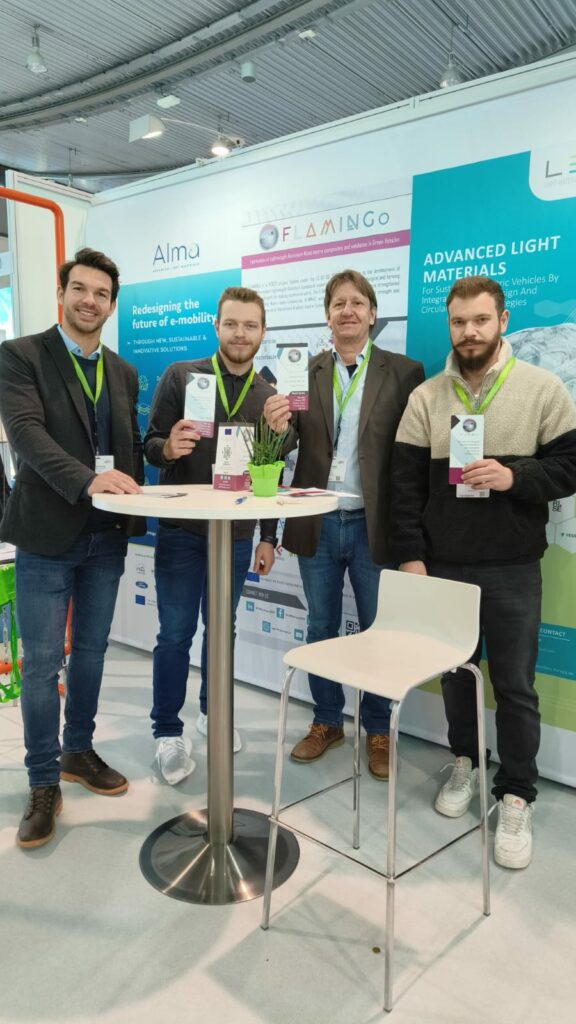

Vasilis Maris, for instance, was asked by a curious visitor about the steering knuckle demo and its implications on lightweighting EVs. In addition, he was also asked about how topology, design and die casting is conducted to achieve lightweighting. This is what he said: “Visitors asked me about how we increase battery and engine power with lighter materials. For example, we changed materials from steel to aluminum metal Matrix nanocomosites (Al-MMnC). Through this process, our concept small electric truck was more lightweight: steering knuckle weight reduction was up to 58% and rear frame around 35%.”
Thomas Pabel from @ÖGI – Österreichisches Gießerei-Institut, one of FLAMINGo partners, explained that the next step is to cast some left and right prototypes of steering knuckles and implement them in that truck after extensive component tests. This will be necessary to get permission for mass production.
Some visitors were also interested to know the ratio of recycled content in the physical demos on display. The REVOLUTION project representatives were asked, for instance, the ratio of recycled content in the rear crash box of their EV.
Nazif Ugur Kaya from VTT, one of REVOLUTION’s project partners, said some visitors were interested to locate the part within the vehicle, and asked about the kind of properties required for rear crash box and how much weight reduction was achieved. Some also asked about the material type and properties.

Here’s what Nazif Ugur Kaya said: “We made a steel replacement with PC-PBT blend for lightweighting and high recycled content, so we have now more than 65% recycled content in the rear crash box and more than 45% lightweighting was achieved. And the final solution is mechanically recyclable. Since it requires safety compliances, it needs high mechanical properties for the rear crash box.”
Carlos Barreto was asked about the innovation on Self Reinforced PP panel for Thermoforming.
He said: “This is a new process that is made with full width films not with the weaving of ribbons. The new process enabled incorporation of high PCR (POST CONSUMER RECYCLATE) content of about 50%. The other innovation was the formulation of PCR itself that together with the process resulted in Self Reinforced PP suitable for flexible and rigid panels that can be used for thermoforming or for skins in sandwich composites.”
Meanwhile, at the Stuttgart Fair, we also bumped into ALMA consortium partners, CTAG – Centro Tecnológico de Automoción de Galicia and Fraunhofer ITWM, at the Interiors Expo and Foam Expo, respectively.


Vanessa Ventosinos Louzao from CTAG described her booth 3616 in summary: “CTAG’s booth is all about smart materials, plastronic, and resonant surfaces! All the solutions presented are very easy to integrate, simple, with any kind of vehicle. It’s an easy way to have new functions.”
Then, we met up with Heiko from Fraunhofer ITWM and asked him about his experience at Fraunhofer ITWM booth 250 at the Foam Expo!
He said visitors were interested to understand the foaming process simulation. “For example, for Lithium-ion batteries, between the cells, one needs a material and one option is foam. Foam density is not constant and homogenous, and thus, Fraunhofer ITWM conducts simulation on micro-scale to take into account anisotropic mechanical behaviour.”
And that’s a wrap!
In summary, the Enlight EVs cluster event at the GACS Expo was a unique opportunity to facilitate knowledge transfer among the sister EU-funded projects but also create collective visibility and engagement for the cluster under the theme “Leading the Way in Innovative and Lightweight EV Components”. Over three days, the cluster booth witnessed frequent footfalls from industry professionals, technology enthusiasts, and curious onlookers who gathered to create an energetic and lively atmosphere that led to organic conversations, coupled with the exchange of innovative ideas.

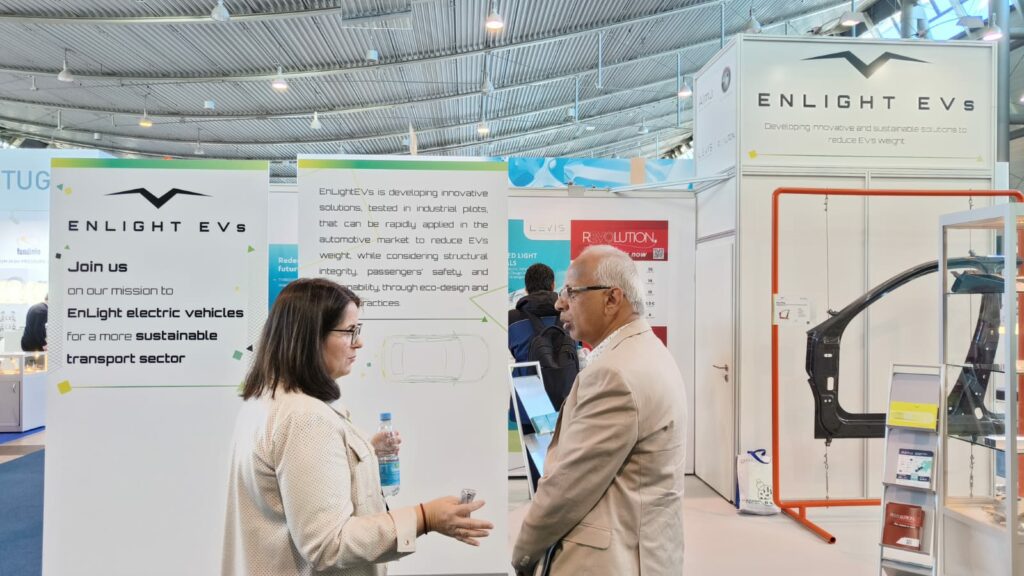

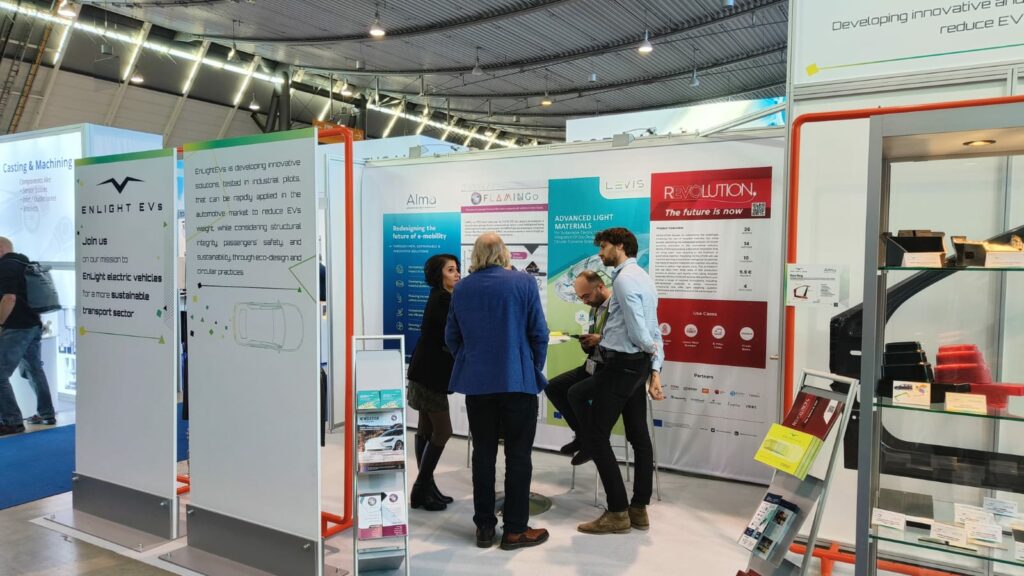
Thanks to all cluster partners – REVOLUTION project, FLAMINGo Project, Greenvehicles LEVIS for this culmination event.
Generous thanks to the European Commission Project Adviser (CINEA – European Climate, Infrastructure and Environment Executive Agency) Salima Abu Jeriban for extending support through her presence at the cluster event.
Last but not the least, a big thanks to the Steinbeis Europa Zentrum team for organising and supporting the Cluster from day 1!

