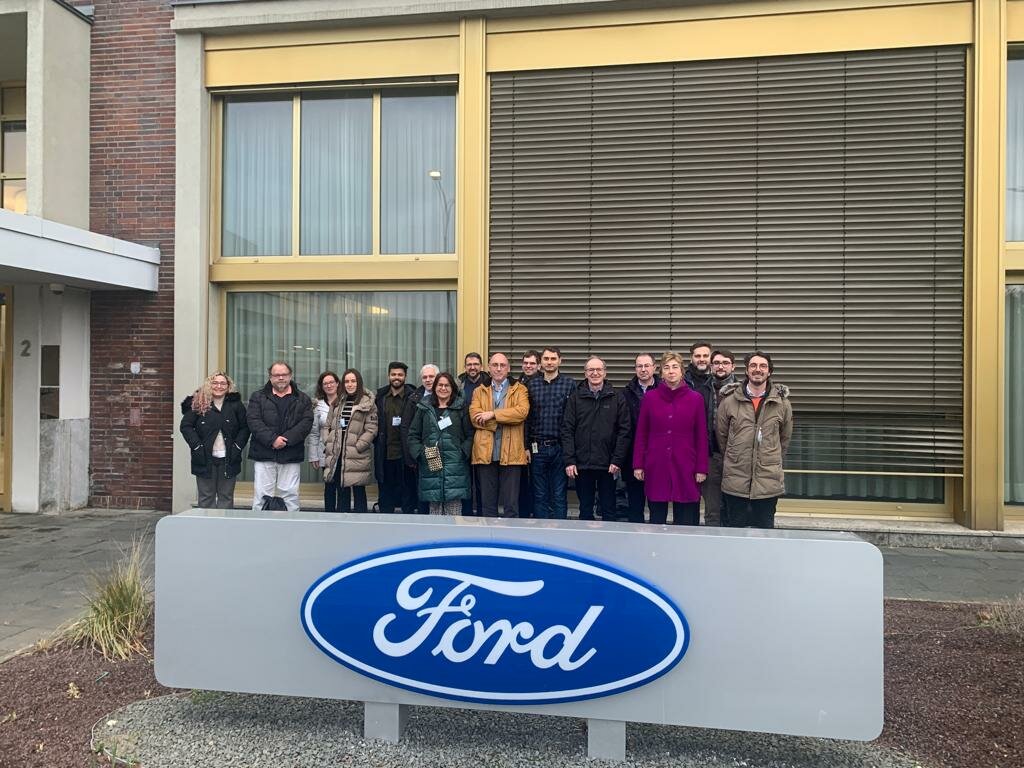
The ALMA Project has concluded, yielding insightful results poised to redefine the future of electric mobility. The ALMA consortium, a group of nine European organisations from four European countries, gathered for the final time for the two-day General Assembly meeting in Cologne, Germany to present a comprehensive overview of the project outcomes and the way forward. Serving as the official host for the General Assembly meeting, Ilya Popov, from consortium partner Ford-Werke, facilitated the sessions.
The main takeaway is that by using an Eco-Design approach and advanced materials, supported by TNO’s BEVSIM tool for Life Cycle Assessment (LCA) and Life Cycle Costing (LCC), the ALMA Battery Electric Vehicle (BEV) body-in-white (BiW) structure achieved a remarkable 22% weight reduction. A noteworthy 160kg lighter car was achieved compared to the baseline BEV BiW design. The integration of advanced materials and weight reduction in the BiW contributed to a total decrease of 1,850 kg in CO2-eq (Carbon dioxide equivalent), resulting in a significant 24% CO2-eq reduction throughout the vehicle’s service life. For the entire car, the CO2-eq reduction was 9%. Due to lightweighting, the vehicle range also increased by 6%.

Raquel Ledo from CTAG presenting project achievements to the consortium and EU Project Officer (CINEA).
These were some of the main highlights from the General Assembly meeting, in which all consortium partners presented their respective achievements in the work packages. European Commission Project Adviser to CINEA Salima Abu Jeriban, who was also present, congratulated the ALMA Project for timely completion. “Congratulations on finishing on time because of Covid-19, but you managed to keep within the three years, so this is quite remarkable,” she said.
WATCH ALMA’s Final Project Video Below

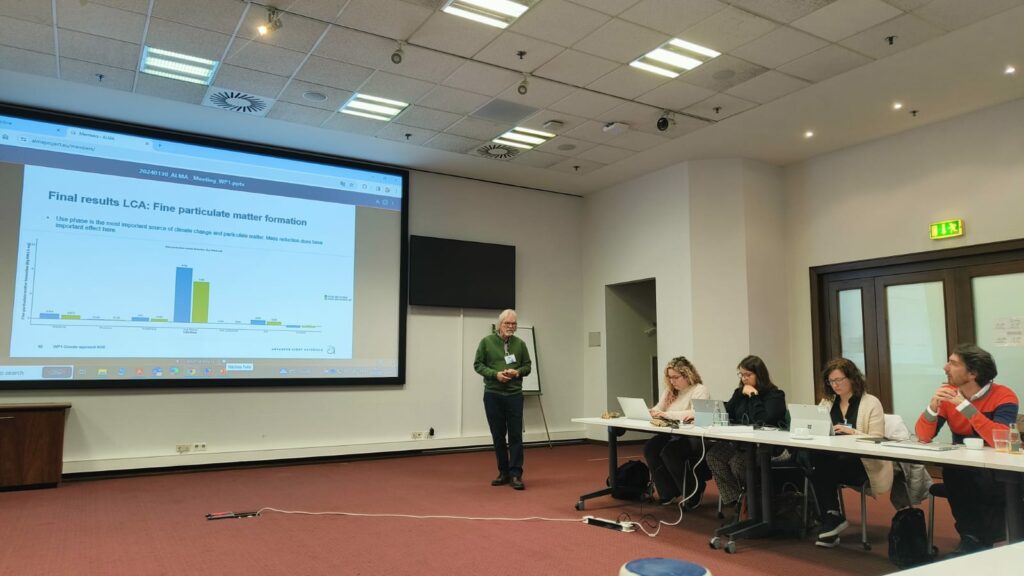


A key exploitable result (KER) of the project is the knowledge generated from our eco-design approach and advanced materials. The results obtained from implementing the eco-design process can inform and inspire future designs, fostering decarbonization in the road transport sector and promoting circular economy principles (reduce, reuse, repair, recycle) in the largely linear (take-make-use-dispose) automotive industry.
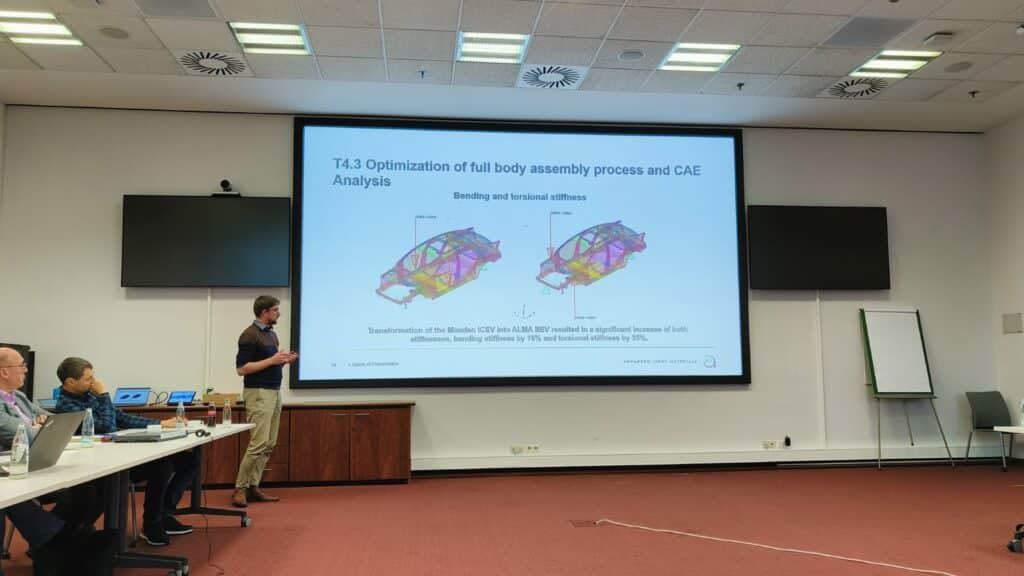

According to the sustainable and smart mobility strategy, the EU aims to have at least 30 million zero-emission vehicles on its roads by 2030 and achieve a 90% reduction in transport-related greenhouse gas emissions by 2050. The ALMA Project’s accomplishment will bolster the bloc’s commitment to decarbonize road transport and promote circular economy approaches in the automotive industry, a sector known for its significant carbon emissions, material intensity, and end-of-life vehicle disposal challenges.
As part of the visit, the consortium also visited the Ford vintage car museum and manufacturing facility that produces the transmission for Ford vans.
During the visit, Ford showcased the ALMA demonstrator in the presence of project officer Salima Abu Jeriban, demonstrating our commitment to bridging vision with reality.


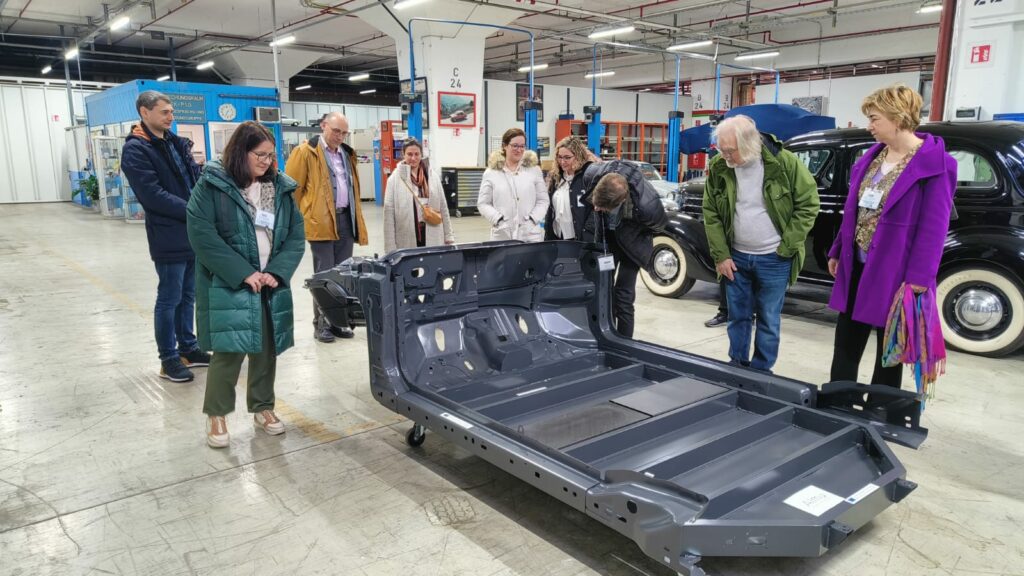



The final meeting caps an eventful 3-year journey replete with challenges and opportunities in developing a battery electric vehicle for passenger car that is lightweight, efficient, and sustainable using an Eco-Design approach and advanced materials.
Although the project has ended, the accomplishments were further showcased at the Road Transport Research (RTR) Conference in Brussels, Belgium between 5-7 February 2024. Consortium partner CTAG presented the ALMA Project results alongside the SALIENT Project in the session on Materials. Enlight EVs cluster partner Fatigue4Light was also present at the session.
In December 2023, the ALMA Project proudly presented its outcomes at the Enlight EVs cluster technology transfer event during the Global Automotive Components and Suppliers (GACS) Expo in Stuttgart, Germany. Consortium partner ArcelorMittal showcased tangible successes through two physical demonstrators – the H-Frame and the Door Ring.
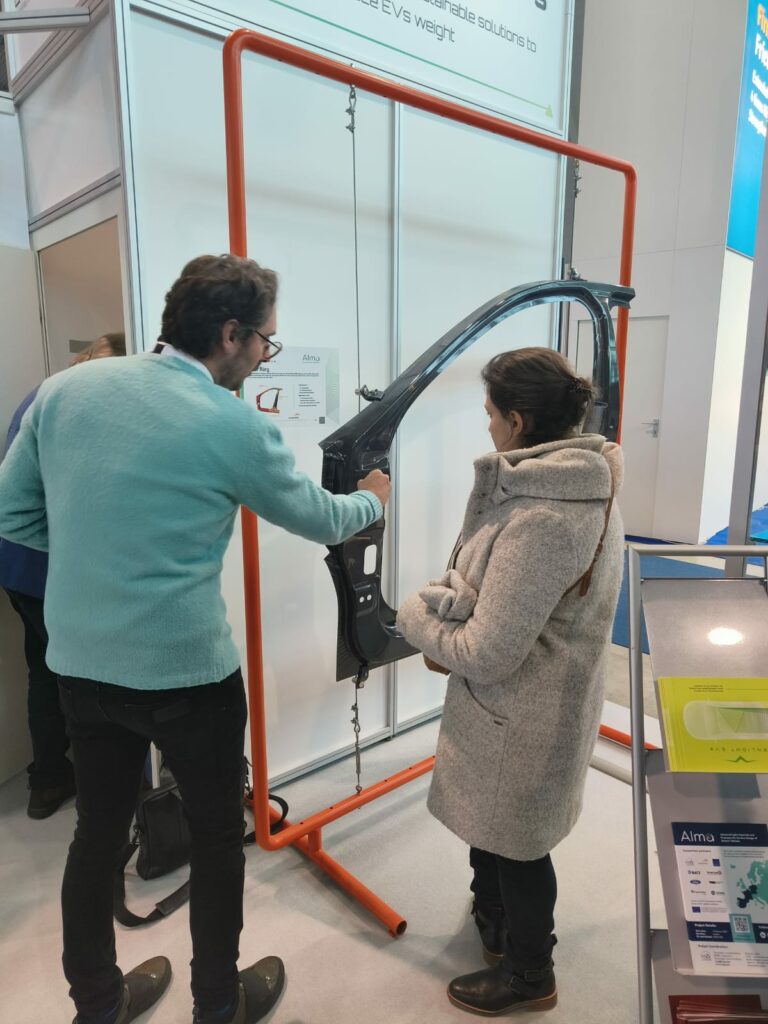

These demonstrators validated efficient manufacturing processes and the Multi-Part Integration concept, employing Laser Welded Blanks technology with the utilization of advanced high-strength steels (AHSS).
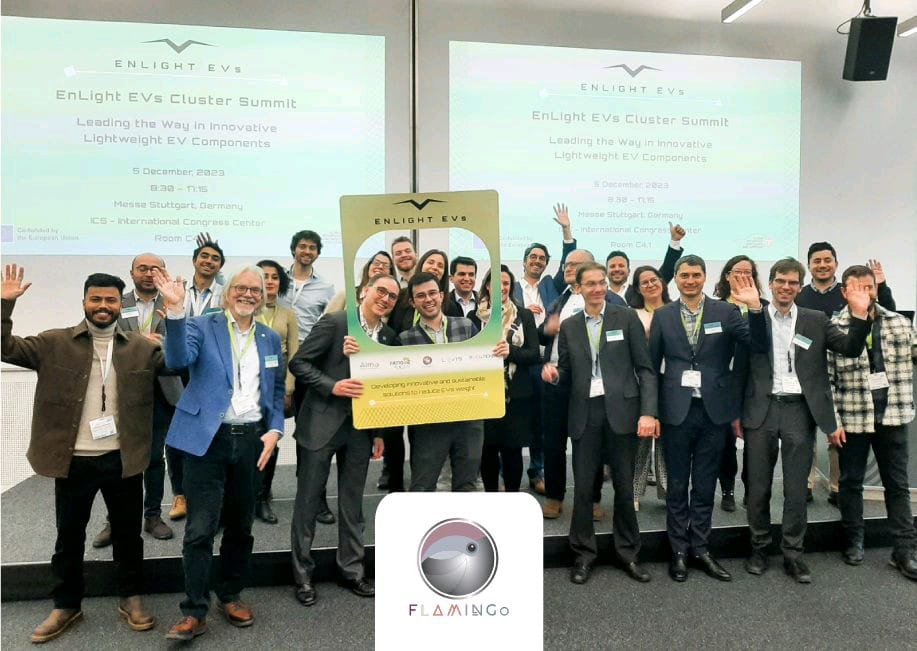

A project brochure was also created to highlight the achievements in brief and showcased at the GACS Expo.
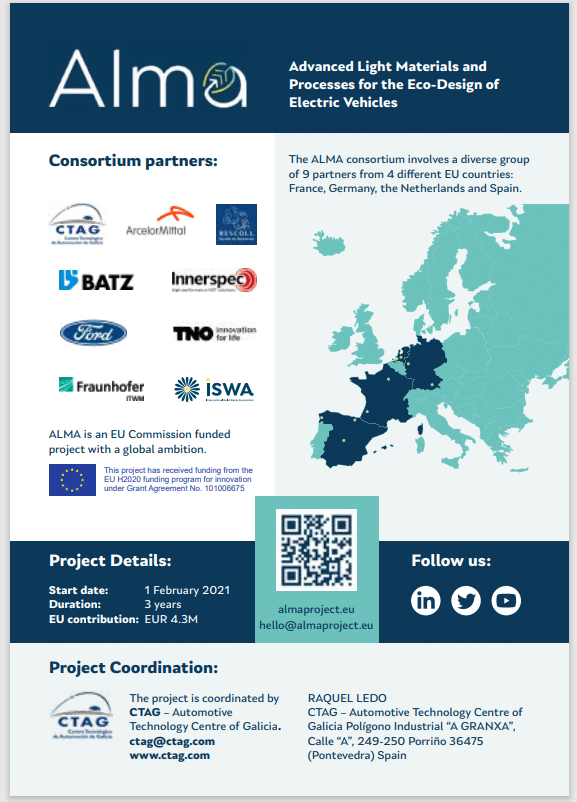
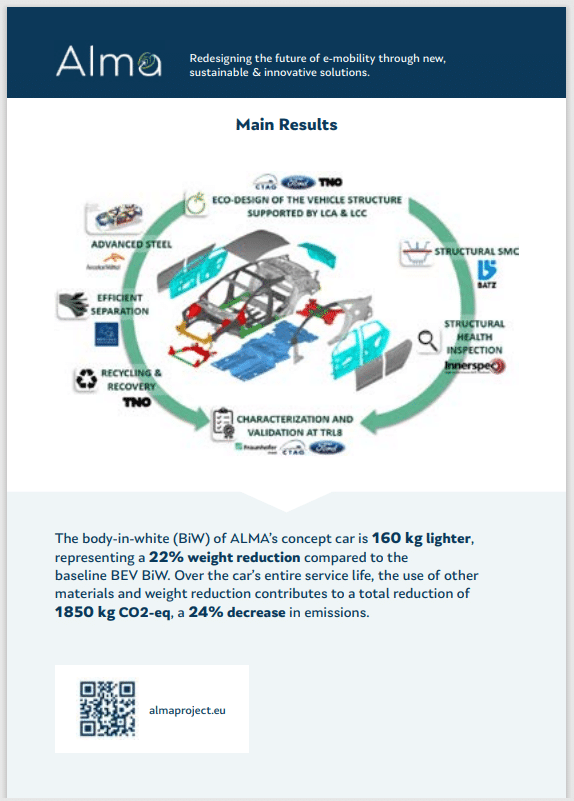
About the ALMA Project
The ALMA Project (Advanced Light Materials and Processes for the Eco-Design of Electric Vehicles) is an EU-funded project under Horizon 2020. The project consortium involves a diverse group of 9 partners from 4 different EU countries: France, Germany, the Netherlands, and Spain.
The group involves five market-orientated companies, three RTOs and one International association; the members of the consortium, led by CTAG – Automotive Technology Centre of Galicia (Spain), include: ArcelorMittal Maizieres Research (France), Ford-Werke (Germany), Innerspec Technologies Europe (Spain), BATZ S. Coop. (Spain), RESCOLL (France), Fraunhofer Gesellschaft zur Förderung der Angewandten Forschung E.V. (Germany), Nederlandse Organisatie voor Toegepast Natuurwetenschappelijk Onderzoek TNO (Netherlands) and ISWA – International Solid Waste Association (Netherlands).

The project’s objective was to improve the efficiency and driving range of electric vehicles (EVs) through sustainable lightweighting of the vehicle structure, saving energy and materials, thereby reducing carbon emissions. Furthermore, increasing environmental awareness and forthcoming stricter regulations demands the adoption of circular economy principles across the entire vehicle life cycle.
This was a three-year project which aimed to achieve innovation and sustainability. To respond to this challenge, ALMA developed a novel battery electric vehicle (BEV) BiW structure for a passenger car with around 22% weight reduction compared to current baseline at affordable costs. Thus, ALMA developed a multi-material modular platform made of a combination of Advanced High Strength Steels, Advanced-SMC and steel-hybrid materials, characterized with multiscale model-based tools.
The Circular Economy was at its core. ALMA adopted circular economy principles from early stages through the application of Eco-Design strategies to create a novel BEV platform “made to be recycled”. For this purpose, it employed a structural reversible bonding technology to enable the separation of components at the end-of-life (EoL) for repair and reuse. An innovative health monitoring system based on acoustic emissions has been integrated in the structure to detect and locate damage while in-service. To complete the circular loop, efficient recycling and material recovery options were analyzed.