The expected promise of battery electric vehicles is mitigating the carbon footprint of driving cars. Indeed, electric vehicles produce no carbon dioxide during driving. But what about the production, maintenance, electricity consumption for battery charging and the eventual disposal of the vehicle? All these things have to be taken into account before we can decide what is better for the environment. This is of course what life cycle assessment (LCA) is all about. LCA is specifically important in assessing lightweighting concepts to improve environmental impact. In general, we can expect that lower vehicle weights can be associated with lower environmental impacts, as lighter vehicles will require less energy to move and using less materials should then also decrease the impact during manufacturing. However, this is not always the case, as reducing the weight can come with materials choices that have production methods with more emissions than the ones they replace.
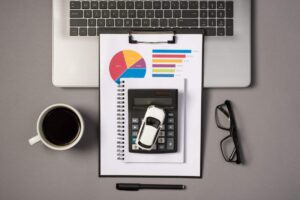
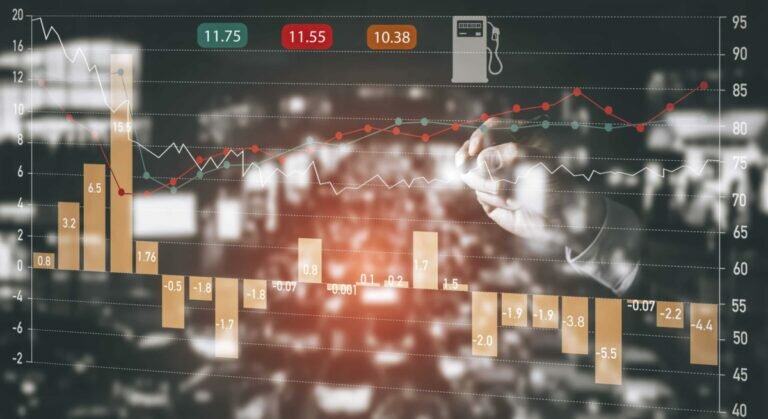
Making the right choices will be even more important as the proportion of the emissions coming from the manufacturing and of end-of-life phases will increase relative to the use phase when we lower the emissions during driving. For traditional internal combustion engines, material production on average represents 15% of the total emissions. When considering more modern plugin hybrids, that figure can rise to 50% of emissions. We expect that as electricity is increasingly derived from renewable energy sources, the life cycle emissions will shift even to 85% of emissions attributable to manufacturing.
So, what is ALMA doing with all of this? Our project is following an LCA validated eco-design methodology, where alternatives are always checked to make sure that possible trade-offs between impacts make sense. This of course requires a lot of LCAs to be done, in particular comparing the different options available. This is why BEVSIM (Battery Electric Vehicle Sustainability Impact Model) was created, that allows a realistic and efficient method of checking what the impacts are of the different design choices at the part, sub-system or vehicle level..
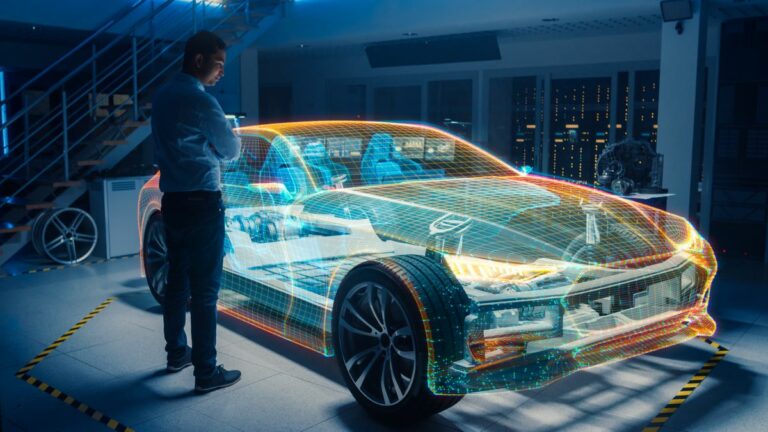
When looking at options to reduce weight, we start by ensuring there is a functional equivalence – not only does it perform like the previous parts during use, but also whether it meet the safety requirements. There is also an assessment made of material utilization rates – how much of the material goes to scrap during manufacture. An evaluation of the emissions for each material must then also include the emissions associated with the production methods, and finally of course we should consider the options and impacts at end-of-life, in other words can the parts be reused, recycled or remanufactured. By combining the observations from all these elements we can evaluate and minimize trade-offs between the impacts of choices at each life cycle phase and make more informed holistic decisions on the best way forward. With this process ALMA has already achieved a more than 20% reduction in the weight of the body-in-white structure, while maintaining the safety and improving the sustainability overall.
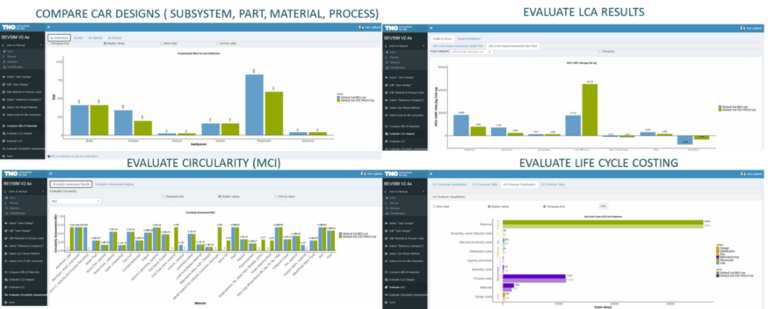
You can learn more about how BEVSIM was developed, how that compares to other approaches and some of the challenges still left to tackle for life cycle analysis in the automotive industry at the upcoming LCA for Automotive Webinar organized by the ALMA and Flamingo projects with the cooperation of the EnlightEV cluster.