
The Enlight EVs Cluster has collectively made significant progress on their respective projects. Cluster partners, ALMA Project, REVOLUTION Project, FLAMINGo Project, Greenvehicles LEVIS, are conducting final validation of their technologies for demonstration at the GACS Expo!
From the start, ALMA picked up the gauntlet to actively promote collaboration for better European Commission-funded project outcomes. Aligned with this commitment, the ALMA project became one of the members of the Enlight EVs Cluster, which was established with the backing of the Horizon 2020 Research and Innovation program grant. In doing so, we have collaborated with other projects funded by the European Commission under H2020, all of which share similar objectives. These objectives focus on advancing sustainable mobility through the introduction of innovative solutions and lightweight materials in electric vehicles.
Since then, the cluster collaboration has focused on expanding the reach of communication and dissemination efforts, providing a comprehensive perspective on recent advancements and opportunities to target audiences. Moreover, the cluster projects have also explored avenues for deeper technical cooperation. As an extension of this united commitment, the cluster will also showcase their respective innovations at the Global Automotive Components and Suppliers (GACS) Expo, 2023 to be held in Stuttgart, Germany from December 5-7.
The purpose of the Enlight EVs cluster is to develop innovative solutions, tested in industrial pilots, that can be rapidly applied in the automotive market to reduce the weight of electric vehicles (EVs), while considering structural integrity, passengers’ safety, and sustainability, through eco-design, topology optimisation, materials’ design and circular practices.
To carry out this objective, the cluster is developing these following solutions to support the automotive sector transition from a linear (take-make-use-dispose) model to a circular (reduce-reuse-recycle) model:
- Advanced lightweight materials and components for EVs
- Recycled lightweight materials and end-of-life strategies
- Physics and AI-based models and sensors for quality control and structural integrity assessment
- Cost-effective manufacturing technologies
- Eco-design strategies supported by innovative LCA tools
- Innovative composite materials
- Strengthened Aluminium nanocomposite for casting, extrusion and welding
Since its inception, the cluster has been consistently working towards delivering on its objectives. Here’s an overview of the cluster’s project progress so far.
FLAMINGo Project updates

- Nano-Additives Production: A cornerstone of the project, nano-additives are vital for Al-MMnC development. These additives are efficiently produced through mechanical alloying, ensuring uniform dispersion of nanoparticles within the aluminum matrix. This achievement opens avenues for incorporating diverse metal/nanoparticle systems into composites, considering both performance metrics and production costs.
- Optimising Casting and Extrusion: Casting and extrusion processes are pivotal in Al-MMnC component manufacturing. FLAMINGo is committed to fine-tuning and refining these processes for top-tier quality and efficiency. The goal is to deliver lightweight and structurally robust components that align seamlessly with green vehicle requirements.
- Topology optimisation: Topology optimization in FLAMINGo serves to enhance the performance of a component with its primary objective is to achieve either weight reduction or enhanced structural stiffness.
- Green Vehicle Integration: Beyond individual component development, FLAMINGo places a strong emphasis on integrating Al-MMnC components into electric vehicles. This integration is more than mere attachment; it involves a deep understanding of how these components interact with other vehicle elements. FLAMINGo dedicates considerable effort to aligning these components with the overall vehicle design, ensuring a harmonious fit that boosts performance and efficiency.
- Economic and Environmental Impact: FLAMINGo’s progress carries substantial economic and environmental significance. The adoption of lightweight Al-MMnC components significantly reduces vehicle weight, enhancing fuel efficiency and curbing carbon emissions. This dual impact is poised to drive sustainable advancements in the automotive industry.
Explore FLAMINGo Project
REVOLUTION Project Update

REVOLUTION project focusses on overcoming the challenges hindering the use of recycled materials, but more broadly, restricting the widespread adoption of circular economy principles in the automotive industry. Forthcoming EV directives are expected to recognize the potential for recycled plastics and to enable a circular flow of materials in the automotive sector. Implementing minimum post-consumer recyclate (PCR) targets in any plastic components in vehicles is currently being discussed.
REVOLUTION aims to demonstrate automotive components, using polymer solutions that feature optimized recycled materials to increase light-weighting opportunities that extend the range and efficiency of Electric Vehicles and improve end-of-life separation of components to facilitate proper dismantling and the material’s reuse, recovery, and recycling. For that purpose, an AI-Platform will use data from three areas of the production process to predict part quality when using recycled materials.
Four uses cases are being developed during the project’s duration:
- Back seat panel: This component is currently made of a formed steel sheet that is welded to a metallic frame. REVOLUTION will build on CRF’s previous efforts to convert this component to a SRPO, with a weight saving of ~55%.
- Lower Rear Bumper: It is a coloured aesthetical part. Many times, it is difficult to attain the appropriate colour and gloss using post-consumer recycled materials and, at the same time, keep mechanical and physical properties.
- B-Pillar Cover: the manufacturing of a 2k dual-part will be transformed into a mono-material injection moulded component using post-industrially recycled PMMA.
- Crash Box: Nowadays, most crash boxes are commercially produced using steel. The rear crash box demonstrated in REVOLUTION will be a 100% polymer solution.
The end of the project is near, and the final phase has started: demonstration and validation of the final components are being run, its degradation and EV range are being tested, end-of-Life strategies are being proved next to the latest LCA results, and the integration of the AI-predictive control algorithm is taking place.
The REVOLUTION team works together for a more sustainable future!

Explore REVOLUTION Project
Greenvehicles LEVIS project update

LEVIS has embarked on its final phase, dedicated to optimizing the innovative manufacturing processes of the demonstrators, implementing structural health monitoring, and completing the final validation. At the two-day M30 general meeting in Bursa, Turkey, hosted by project partners Yeşilova and TOFAŞ, the inaugural prototypes of various LEVIS demonstrators took center stage for evaluation. These included a suspension arm, a battery box set, and a steering column carrier group.
Within LEVIS, Yeşilova plays a central role involving the complete battery case design, the manufacturing of aluminum components, assembly, and overseeing virtual validation. This is further complemented by conducting physical material characterization tests.
During the second day of the meeting, the LEVIS project members were hosted by TOFAŞ, a prominent automotive company in Turkey known for its production of passenger cars and light commercial vehicles. TOFAŞ contributes significantly to LEVIS across multiple dimensions, encompassing part design, virtual verification tests, physical part production, and the verification of prototype components.

Explore Greenvehicles LEVIS project
Fatigue4Light project updates
Fatigue4Light is a European project coordinated by CIMNE with the aim at developing new tests and computer simulation methods to better estimate the fatigue life of chassis components and to select the optimal materials for lighter vehicle chassis. The project, started last February 2021, is working on the application of new materials tailored to the requirements of vehicle chassis, such as advanced high-strength steels, special automotive stainless steels, high-strength aluminium alloys and hybrid metal-fibre reinforced polymeric materials.
The main goal of the project is to reduce vehicle chassis weight compared to the current solutions existing in the market, taking into account eco-design and circular economy aspects and ensuring optimal fatigue performance.
The Fatigue4Light project has the ambition to help build a zero-emission future by promoting design based on numerical simulation tool. The application of numerical simulation tools at a design stage can help to predict and ensure part performance, as well as minimise production losses by meeting the industry needs.
Fatigue4Light is one of the first projects tackling weight reduction in automotive chassis parts, which is a necessary step to further progress in electric vehicle lightweighting, as reduction of vehicle weight impacts positively in CO2 emissions, electric vehicle autonomy, driveability and security.

The consortium of the project is formed by Eurecat, the International Centre for Numerical Methods in Engineering (CIMNE), the Research and Innovation Centre of Sweden (RISE), the Lulea University of Technology, the Polytechnic University of Catalonia (UPC), the Politecnico di Torino (POLITO), ArcelorMittal, Profilglass, Centre Ricerche Fiat (CRF), Magnetto Wheels (MW), Composite Service Europe, Gestamp and the Spanish Association for Standardisation UNE.
Explore Fatigue4Light project
ALMA Project Updates

As we are nearing the finish line, it is an opportune time to highlight and reflect on the project progress till now. Following the meetup in Brussels last year, the consortium met again in Petten, The Netherlands earlier this year to discuss the project development. Indeed, progress has been made on several fronts.
One of the main achievements is the concept car’s remarkable mass reduction of 160,5 kg, representing 22% weight savings compared to the baseline BEV.

The resulting total carbon footprint was also reduced from 43.5 to 27.8 kg CO2-eq, a reduction of 36%!
Explore ALMA project
Meanwhile, the Enlight EVs cluster partners are going to be present at the Global Automotive Components and Suppliers (GACS) Expo 2023 in Stuttgart, Germany.
If you’d like to register for the event, click here
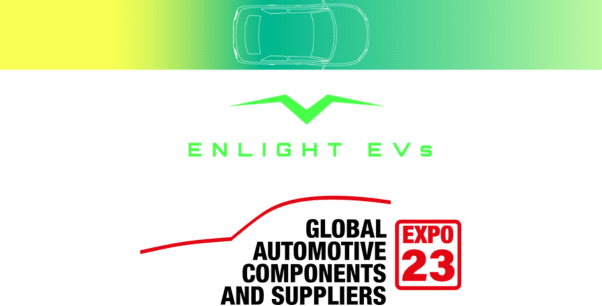